XGSleeve: Real-time monitoring of fracture operations from surface
XGSleeve is an AI-powered breakthrough that detects costly sleeve failures in real-time during fracking which boosting efficiency, cutting waste, and replacing downhole cameras with smart data.
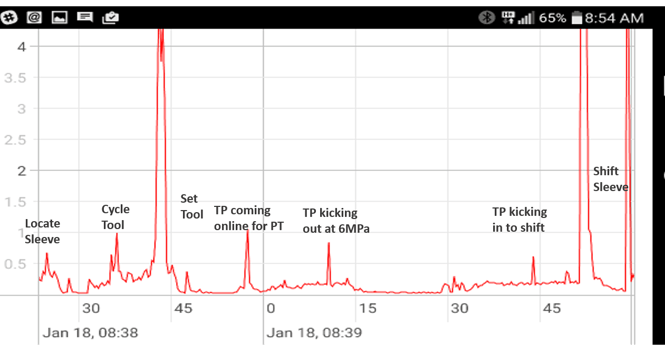
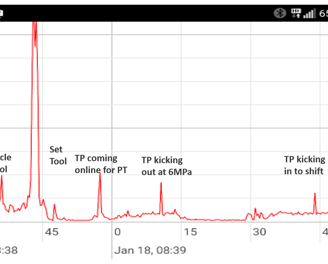
Technical Overview
The Problem
In the oil and gas industry, sliding sleeves are used to control fluid flow during hydraulic fracturing. However, these sleeves frequently fail to open properly, leading to wasted time, materials, and expensive trial-and-error efforts. Traditionally, operators have relied on downhole cameras to verify sleeve operations, but these are costly and not always practical.
The Innovation
XGSleeve is an AI-based system that replaces the need for downhole cameras. By analyzing pressure and vibration data collected during operations, it can detect failed sleeve openings in real-time. This allows operators to respond immediately, improving safety and reducing costs.
Key Benefits
Cost savings by avoiding failed sleeve operations that can cost up to $100,000 each
Real-time alerts provide immediate operational insight
Uses existing field data, requiring no additional hardware
Reduces delays and improves overall operational efficiency
Minimizes resource waste, supporting more sustainable practices
How It Works
XGSleeve monitors the wellhead for subtle patterns in vibration and pressure data. Using advanced machine learning techniques, it identifies signs that a sleeve has failed to open. The system then notifies field operators so they can make informed decisions without relying on visual confirmation tools.
My Role
I developed the machine learning engine behind XGSleeve, including data processing, feature engineering, model development, and performance optimization. I ensured that the system is accurate, efficient, and suitable for real-world deployment.
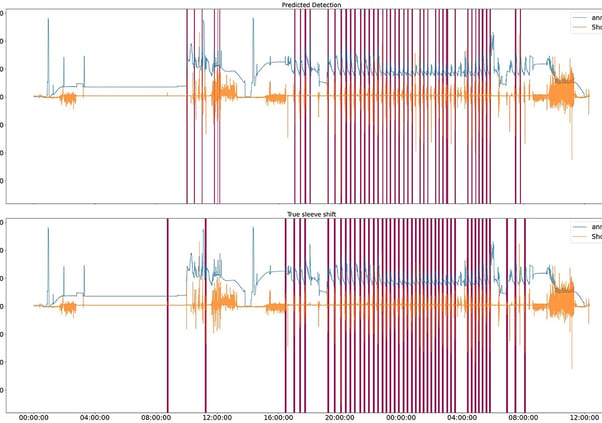
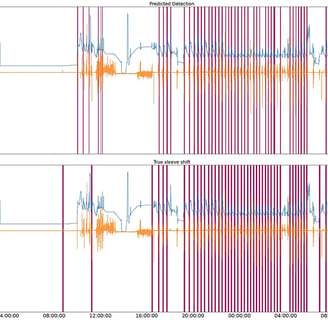